人間とコンピュータとの相互作用の研究
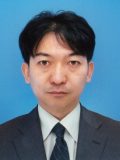
- 工学部 コンピュータ理工学科担当
- 准教授 小俣 昌樹
- ホームページ »
- 山梨大学研究者総覧へ »
40年ほど前,コンピュータを操作するためには,一部の限られた専門家にしか理解できないとても難しい知識が必要でした.現在では,さまざまな人がさまざまな業務を遂行するためにコンピュータを使用しています.このようなコンピュータの発展には,コンピュータをより使いやすくするための「人間とコンピュータとの相互作用」の研究が重要です.
「人間とコンピュータとの相互作用」の研究では,使うのに安全で効率的であり,かつ簡単で楽しいコンピュータシステムを開発しています.現在,いろいろな場面でコンピュータを使用しているにもかかわらず,まだまだ使いにくいコンピュータシステムがたくさんあります.たとえば,パソコンを使って絵を描こうとしてはじめに複雑な操作方法を学ばなければならなかったり,スマートフォンの新しい機能を使おうとして操作方法がわからずにとまどったりした経験のある人もいるはずです.
私たちは,もっと楽しくて使いやすいコンピュータを目指して,以下のような研究を行っています.
・ユーザの生体信号をコンピュータへの入力とし,コンピュータに身体動作や感情を理解させる研究
・ユーザの生体信号を分析して,コンピュータの使いやすさを評価する研究
・触覚,力覚,香りなどを使ったコンピュータとの相互作用に関する研究
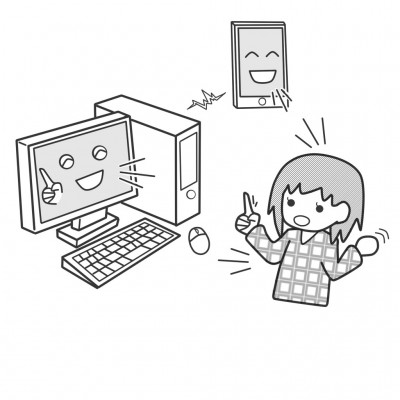